The pdf in the link below contains instructions and technical drawings for the manufacture of probangs. The instructions are repeated below on this page.
Original Document and technical drawings
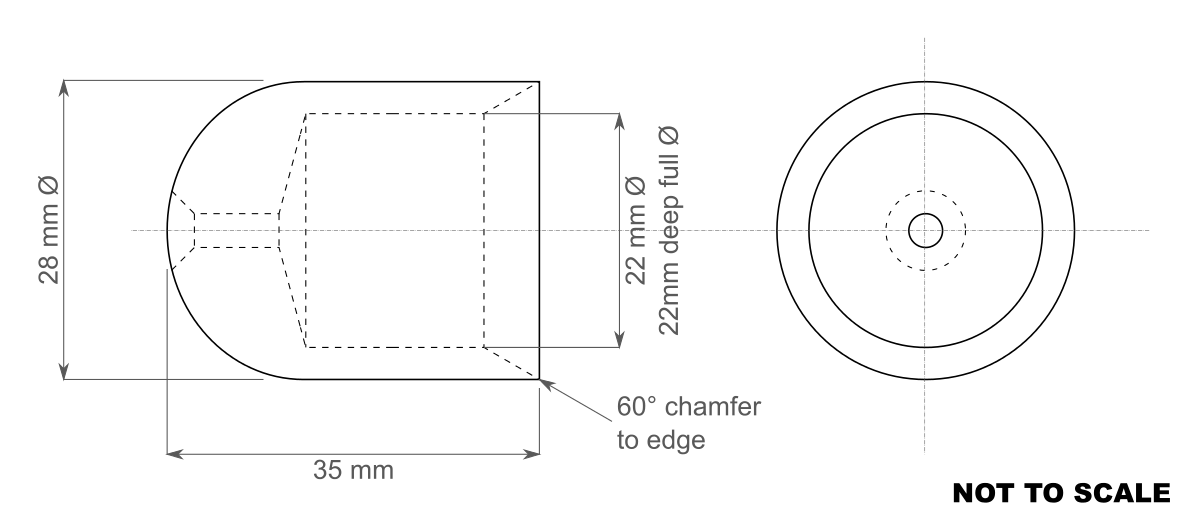
Cup
The cup is turned from free cutting brass stock diameter 7/8 inch (22 mm) for calf probang and 1 1/8 inch (28 mm) for the cattle. Machining sequence as follows:
- Mount in chuck, face, centre drill.
- Pilot drill to full depth, finish drill to drawing.
- Bore chamfer at 60° to edge, remove sharp edge to provide scraping not cutting edge.
- Part off to drawing.
- Reverse in chuck, centre drill, drill through No 30 diameter and countersink to 1/4 inch (6 mm) diameter.
- Turn profile with form tool and blend by hand with fine emery cloth.
Wire Handle
The handle material for all probangs is 10 S.W.G. stainless steel wire in a hard drawn state to provide 'spring'. It is an advantage to have this supplied in coil form so that the handle follows the natural curve of the wire coil.
The first operation, at this stage of manufacture, is to cut to length and form an eye at one end as per drawing. The rivet head will be formed later during assembly.
Assembly
Proceed as follows:
- Slide brass cup, cattle or calf size down the wire.
- Mount wire in head forming fixture and form head. This operation is simplified if the wire is locally heated to red before hammering into shape.
- Clean off heating discolouration from around rivet head, flux area with 'Easy flo' silver solder flux and slide cup into position.
- Silver solder in position, quench and allow to soak to remove flux residue.
Finishing and Final Assembly
Excess solder and any wire that protrudes from the end of the cup is filed and hand polished to blend with the cup profile. The final finish to the whole outside of the cup is achieved with a cloth buffing wheel.
To complete the assembly, a loop of brass safety chain is passed through the eye in the wire handle, as per sketch.
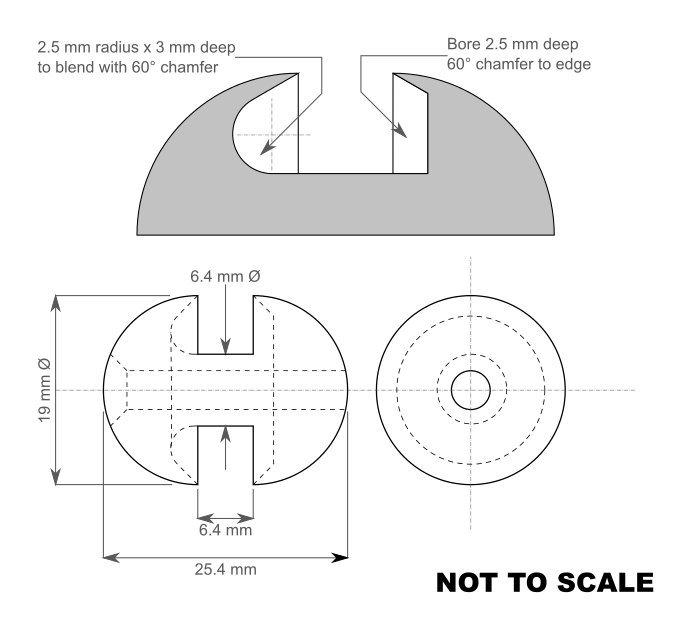
Head
The head is turned from free cutting brass, stock diameter 3/4 inch (19 mm). Machining sequence as follows:
- Mount bar in chuck, face and centre drill.
- Drill No 30 diameter to 1 1/4 inch (32 mm) deep, countersink to 1/4 inch ( 6 .4 mm) diameter.
- Turn profile with form tool and blend by hand with fine emery cloth.
- Plunge centre groove 1/4 inch (6.4 mm) wide x 1/4 inch (6.4 mm) deep.
- Bore recesses with form tools as per drawing.
- Part off to 1 inch (25.4 mm) long.
- Reverse in chuck, mount in chuck fixture and turn other profile, see fixture sketch.
Wire Handle
The handle material for all probangs is 10 S.W.G. stainless steel wire in a hard drawn state to provide 'spring'. It is an advantage to have this supplied in coil form so that the handle follows the natural curve of the wire coil.
The first operation, at this stage of manufacture, is to cut to length and form an eye at one end as per drawing. The rivet head will be formed later during assembly.
Assembly
Proceed as follows:
- Slide brass cup, cattle or calf size down the wire.
- Mount wire in head forming fixture and form head. This operation is simplified if the wire is locally heated to red before hammering into shape.
- Clean off heating discolouration from around rivet head, flux area with 'Easy flo' silver solder flux and slide cup into position.
- Silver solder in position, quench and allow to soak to remove flux residue.
Finishing and Final Assembly
Excess solder and any wire that protrudes from the end of the cup is filed and hand polished to blend with the cup profile. The final finish to the whole outside of the cup is achieved with a cloth buffing wheel.
To complete the assembly, a loop of brass safety chain is passed through the eye in the wire handle, as per sketch.